Sony wm gx 788 service manual
This is the 30 pages manual for sony wm gx 788 service manual.
Read or download the pdf for free. If you want to contribute, please upload pdfs to audioservicemanuals.wetransfer.com.
Page: 1 / 30
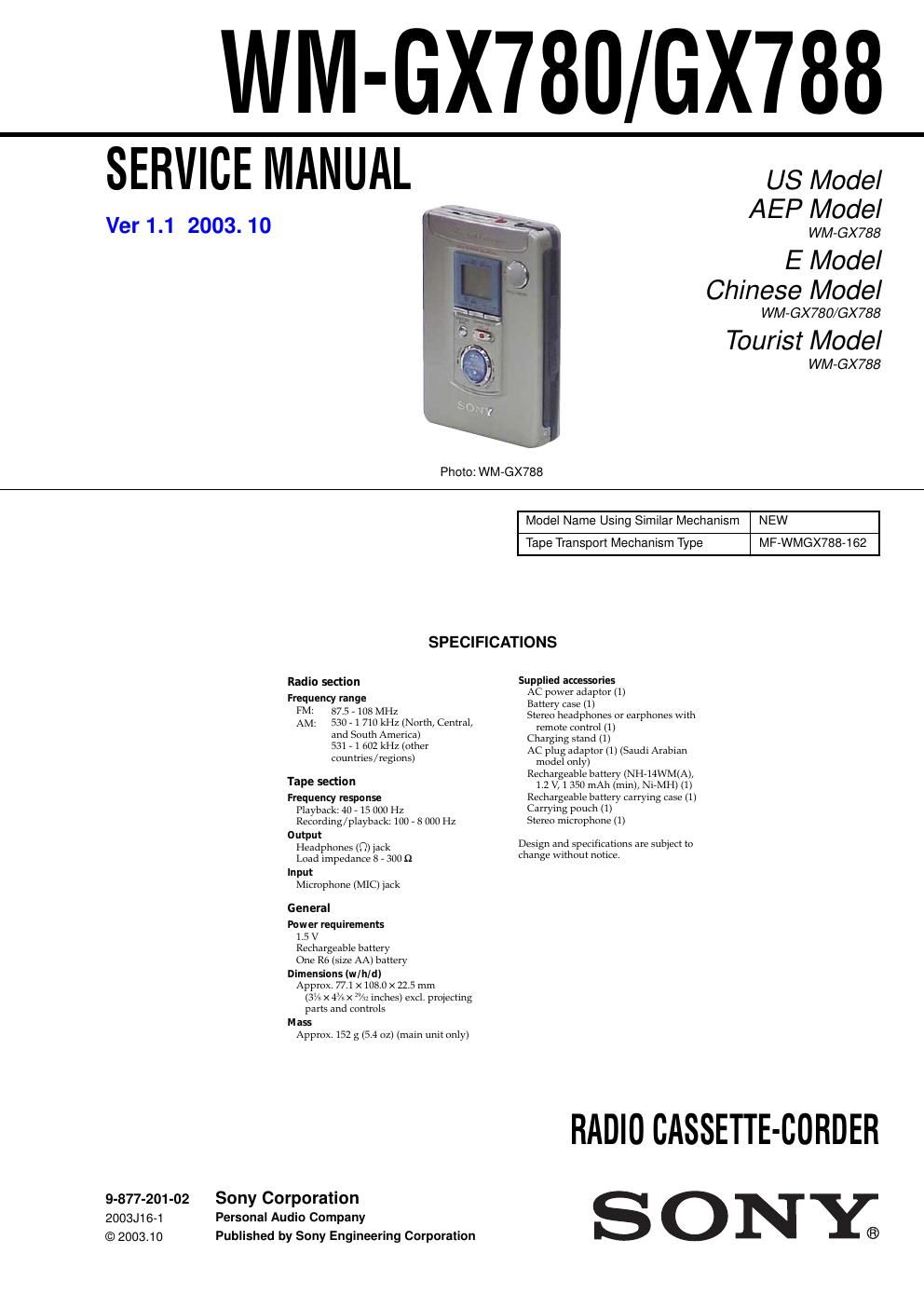