Onkyo MD 185 X Service Manual
This is the 32 pages manual for Onkyo MD 185 X Service Manual.
Read or download the pdf for free. If you want to contribute, please upload pdfs to audioservicemanuals.wetransfer.com.
Page: 1 / 32
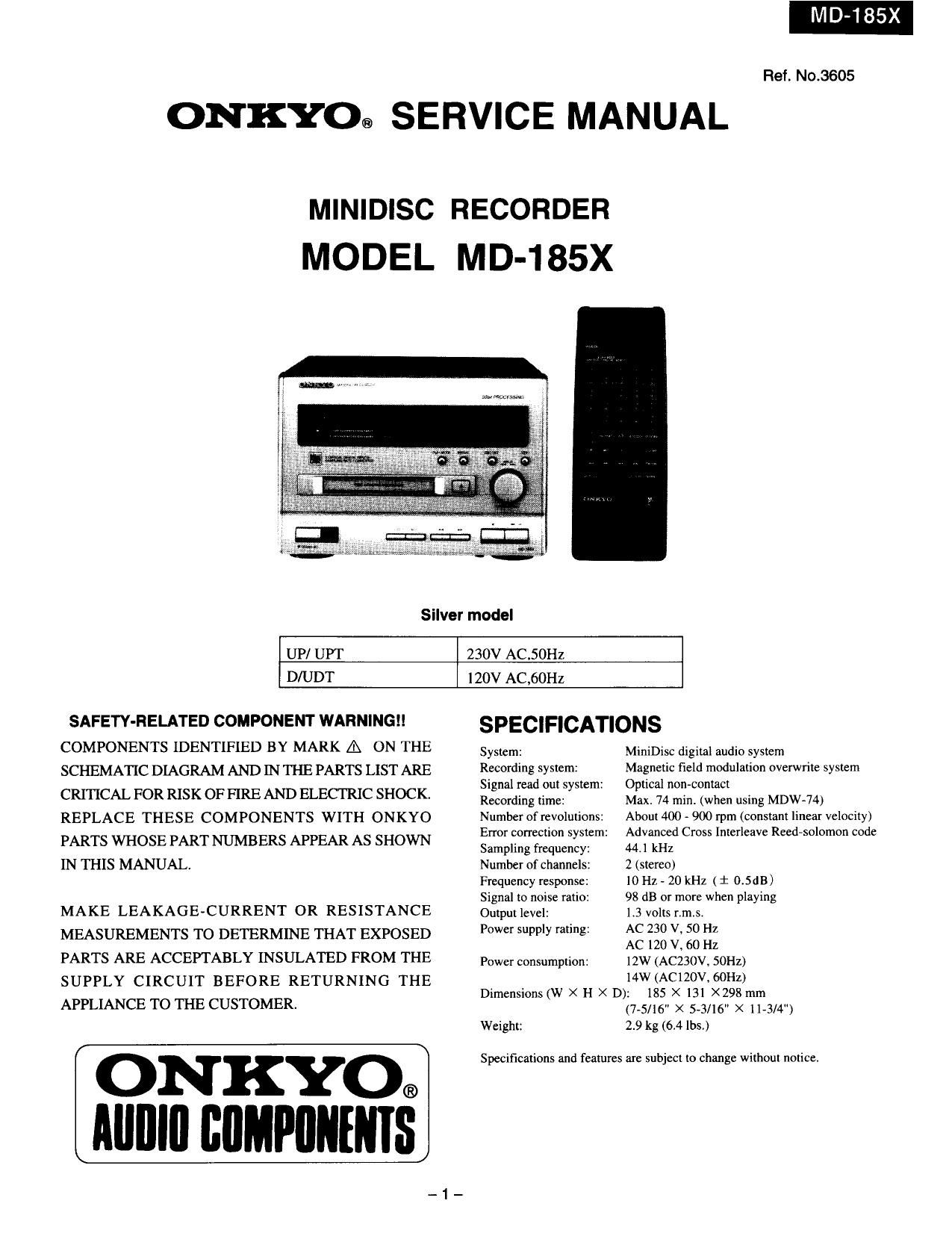