Onkyo DXC 230 Service Manual
This is the 34 pages manual for Onkyo DXC 230 Service Manual.
Read or download the pdf for free. If you want to contribute, please upload pdfs to audioservicemanuals.wetransfer.com.
Page: 1 / 34
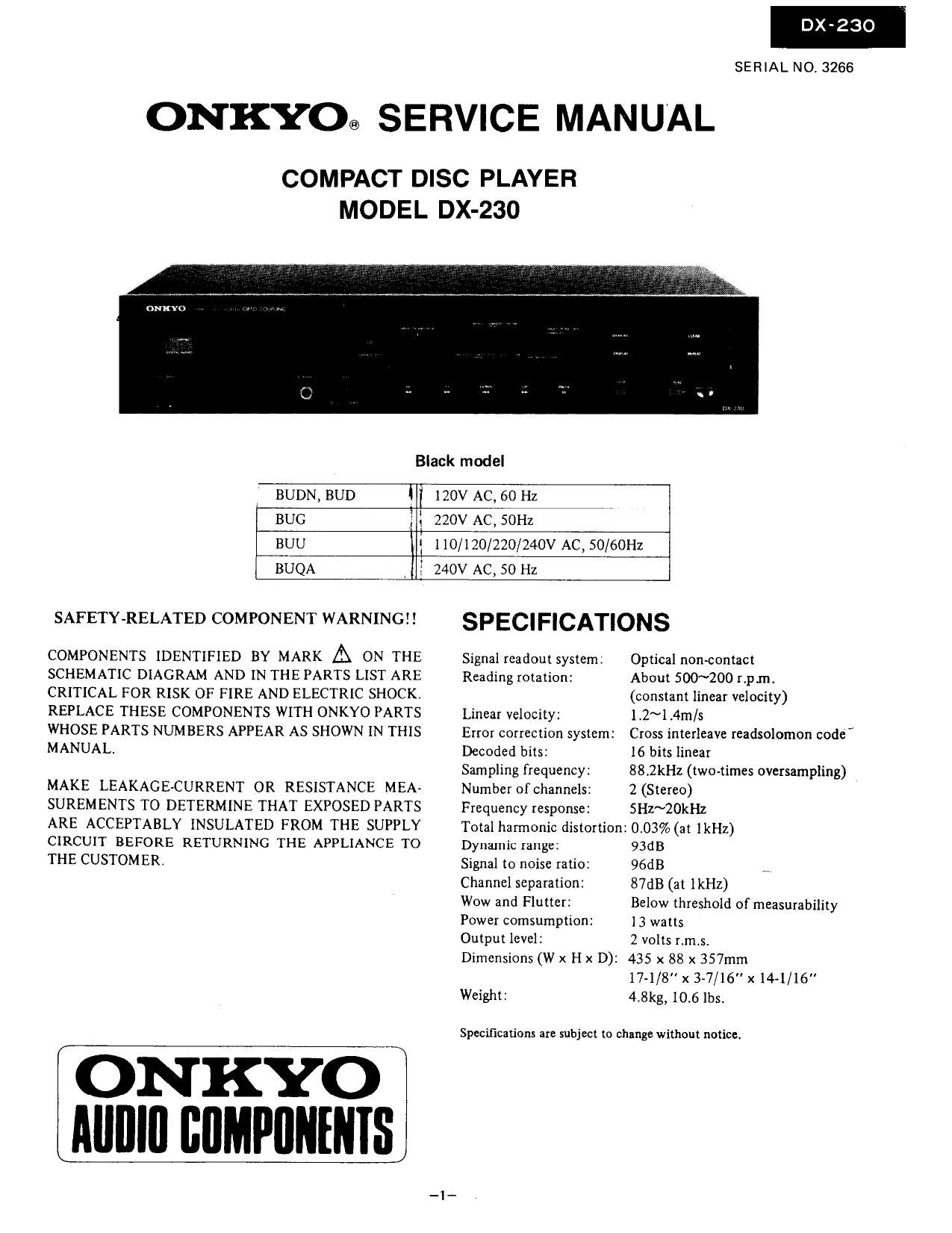