Onkyo DXC 211 Service Manual
This is the 20 pages manual for Onkyo DXC 211 Service Manual.
Read or download the pdf for free. If you want to contribute, please upload pdfs to audioservicemanuals.wetransfer.com.
Page: 1 / 20
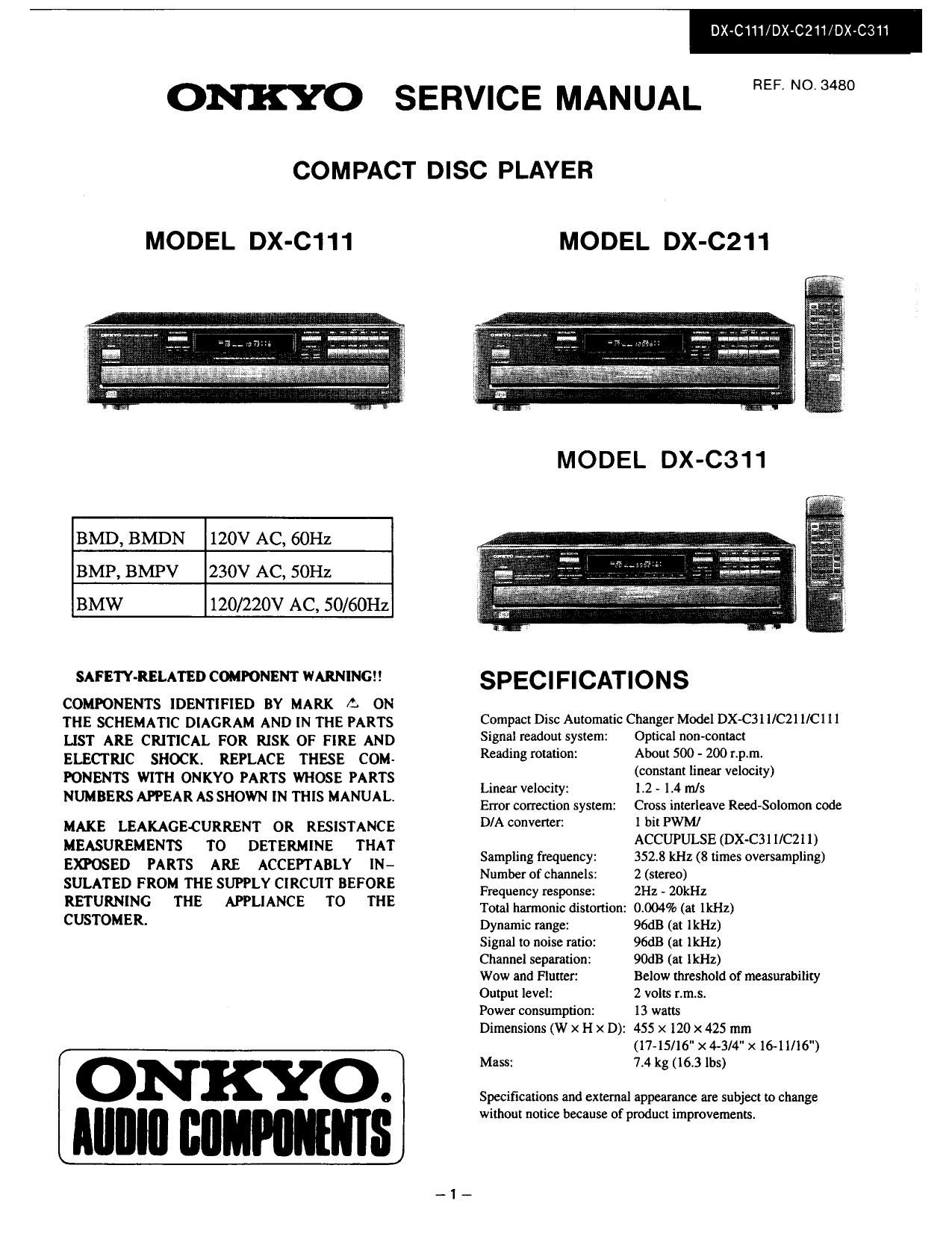