Mackie SWA1801 Service Notes
This is the 3 pages manual for Mackie SWA1801 Service Notes.
Read or download the pdf for free. If you want to contribute, please upload pdfs to audioservicemanuals.wetransfer.com.
Page: 1 / 3
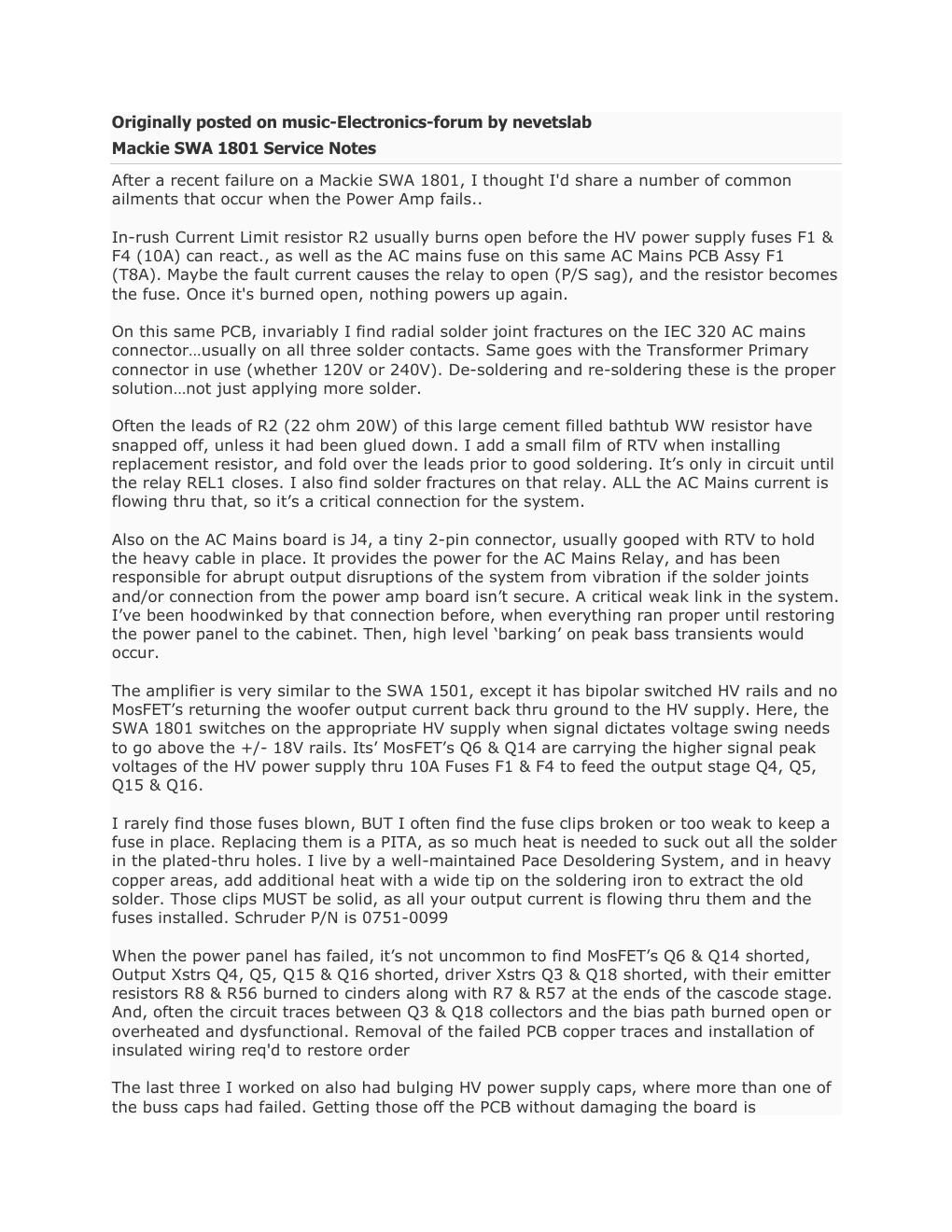