Jvc XMPX 70 WT Service Manual
This is the 38 pages manual for Jvc XMPX 70 WT Service Manual.
Read or download the pdf for free. If you want to contribute, please upload pdfs to audioservicemanuals.wetransfer.com.
Page: 1 / 38
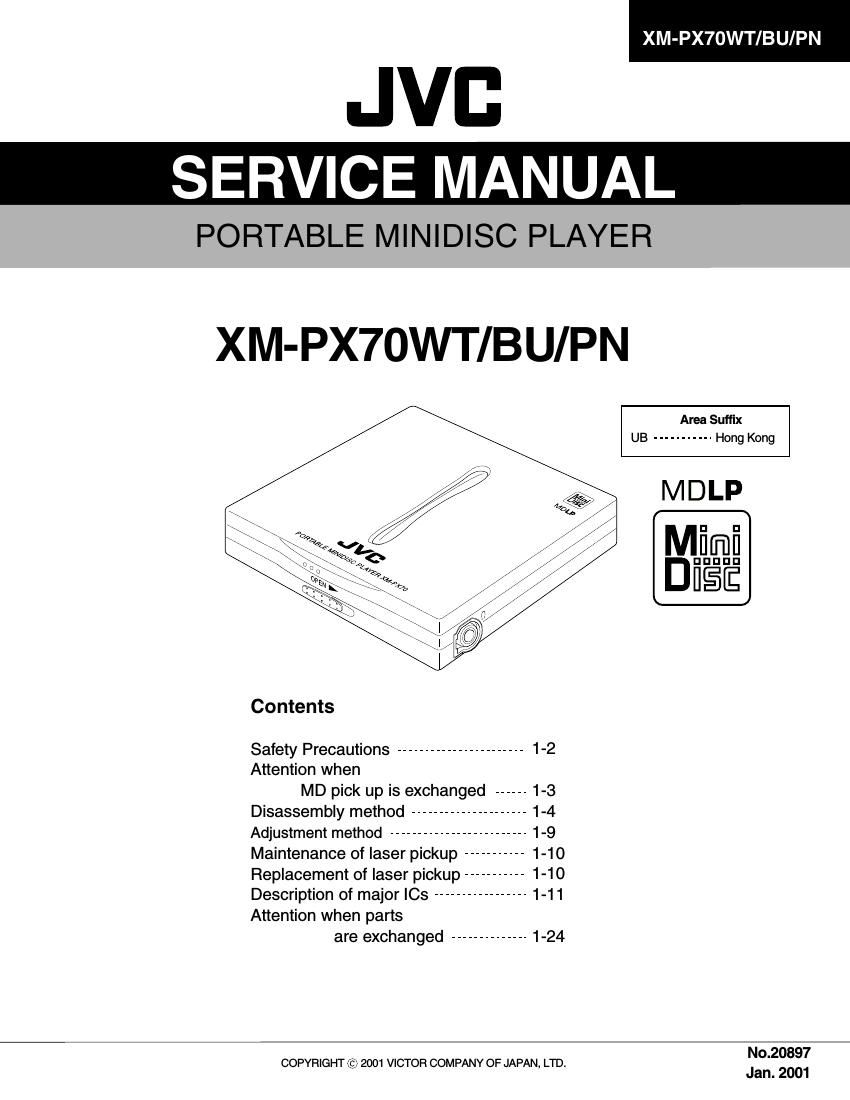