Jvc THA 10 R Service Manual
This is the 128 pages manual for Jvc THA 10 R Service Manual.
Read or download the pdf for free. If you want to contribute, please upload pdfs to audioservicemanuals.wetransfer.com.
Page: 1 / 128
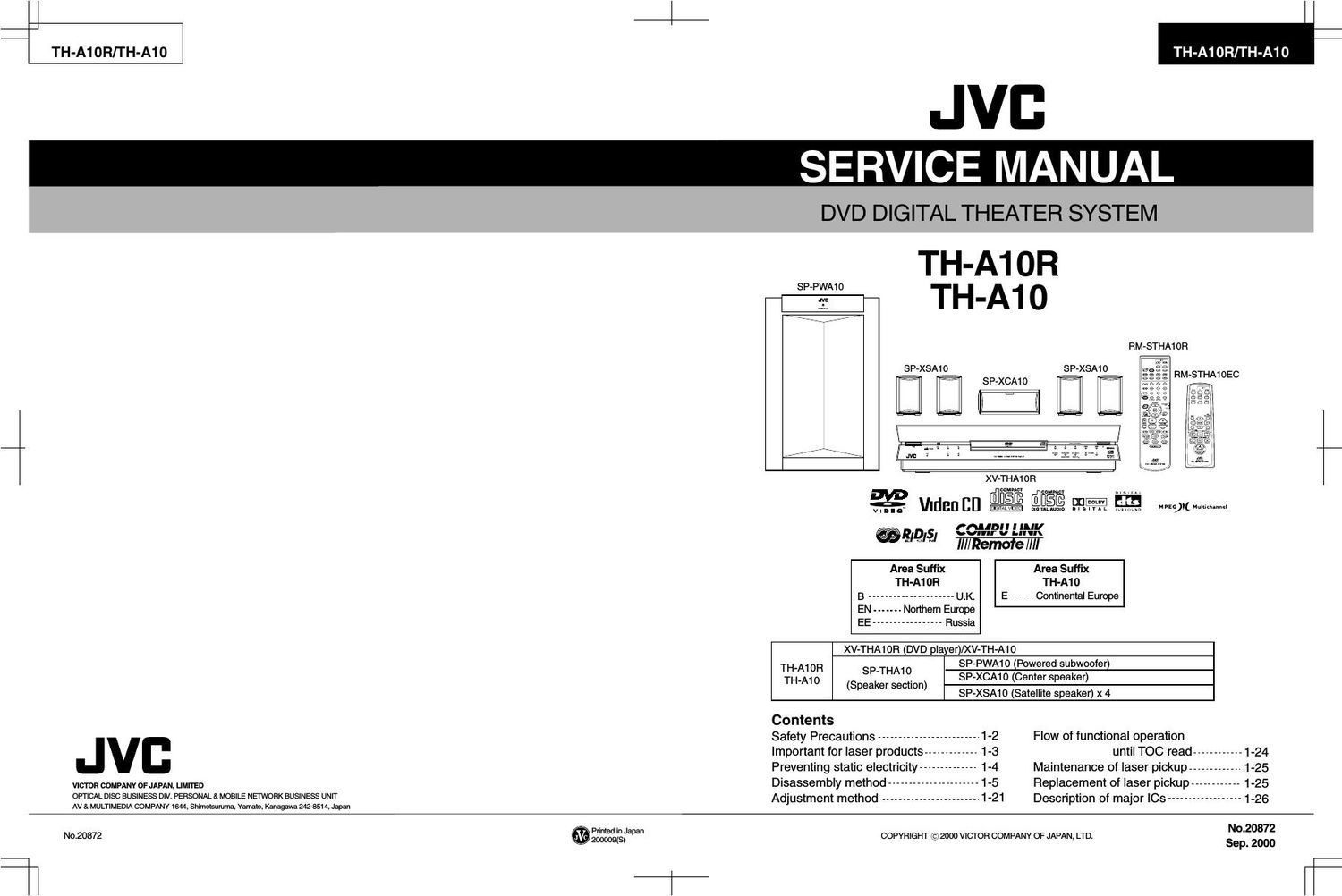