Jvc TDW 315 TN Service Manual
This is the 50 pages manual for Jvc TDW 315 TN Service Manual.
Read or download the pdf for free. If you want to contribute, please upload pdfs to audioservicemanuals.wetransfer.com.
Page: 1 / 50
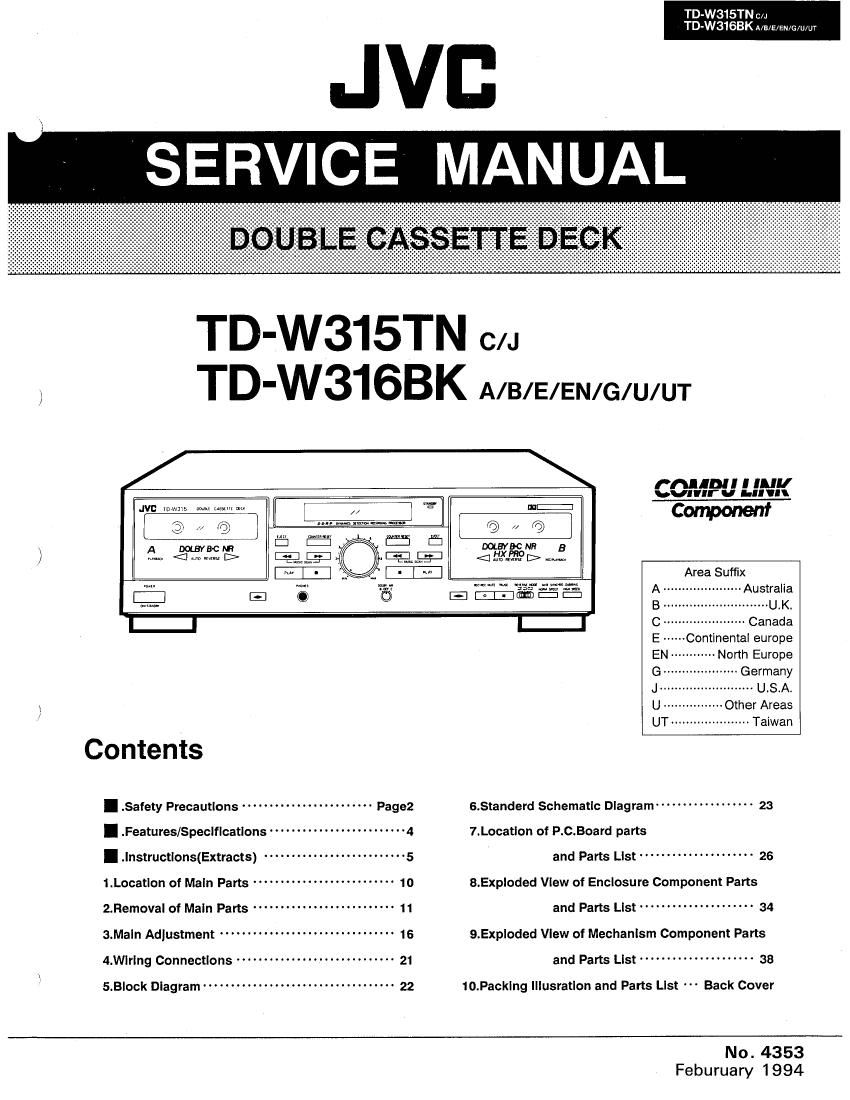