Jvc TDV 562 BK Service Manual
This is the 48 pages manual for Jvc TDV 562 BK Service Manual.
Read or download the pdf for free. If you want to contribute, please upload pdfs to audioservicemanuals.wetransfer.com.
Page: 1 / 48
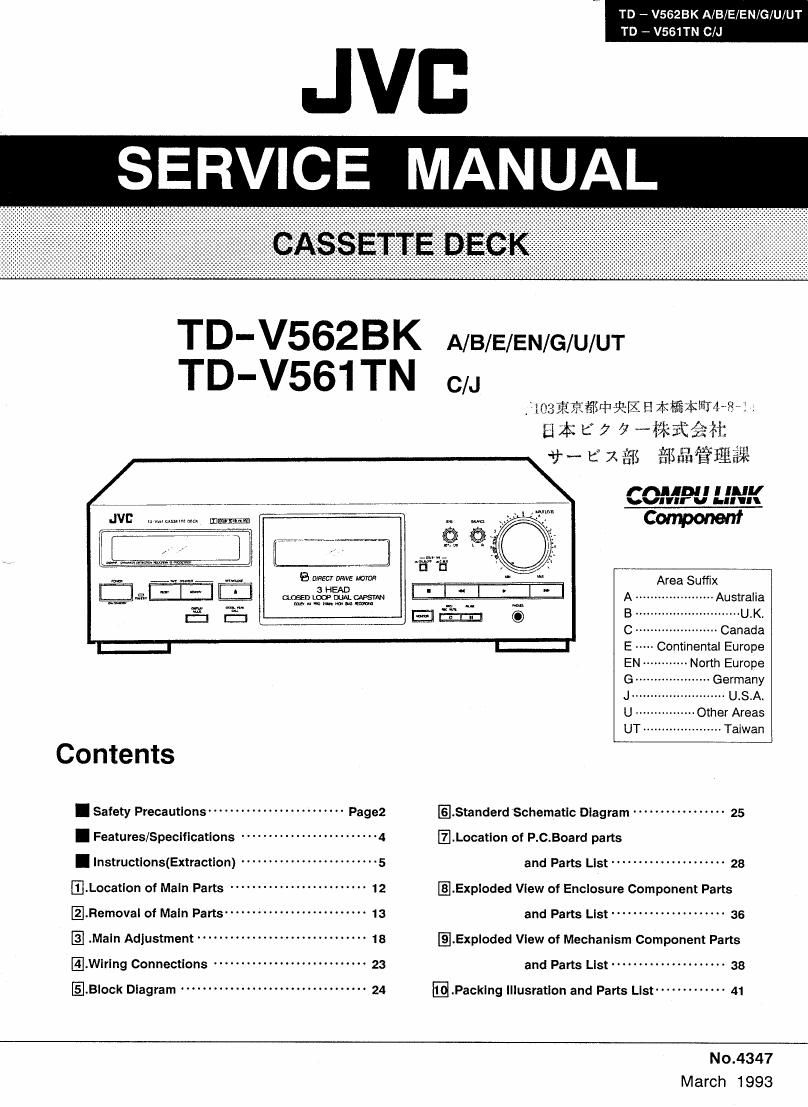