Jvc SPD 752 Service Manual
This is the 134 pages manual for Jvc SPD 752 Service Manual.
Read or download the pdf for free. If you want to contribute, please upload pdfs to audioservicemanuals.wetransfer.com.
Page: 1 / 134
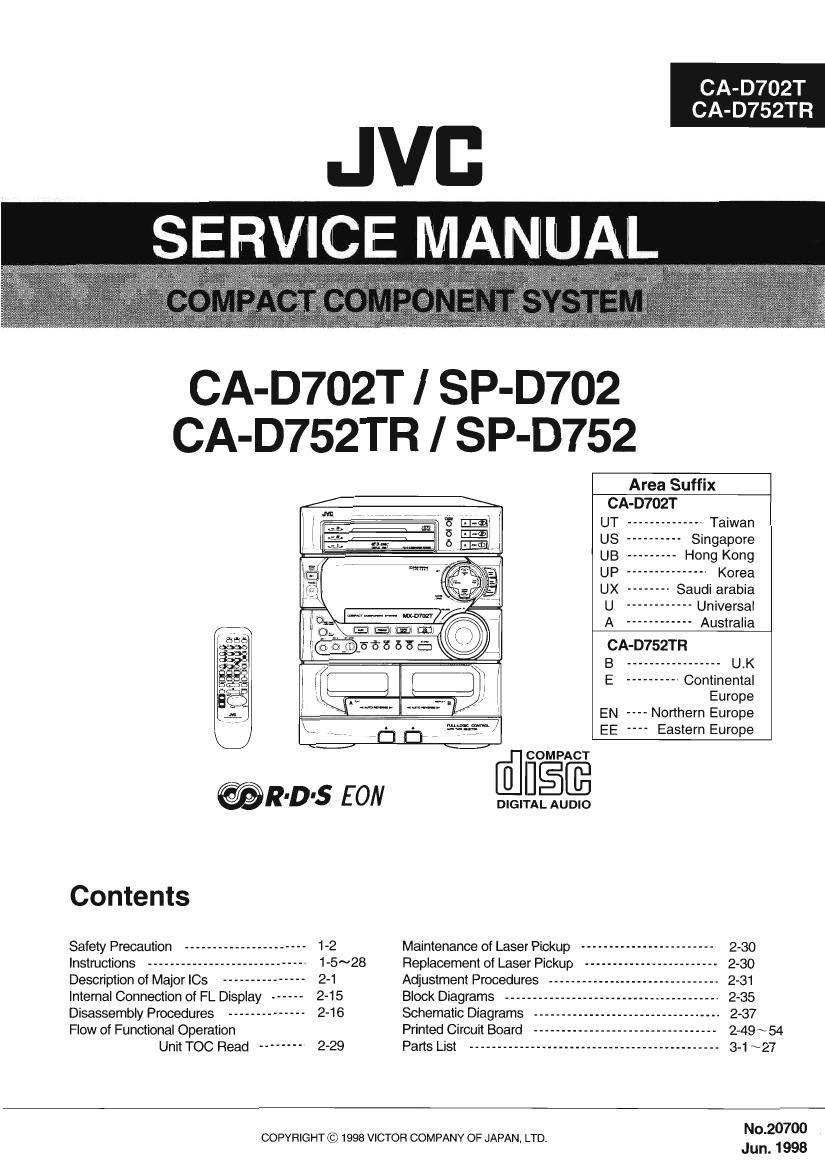