Jvc RXDV 31 SL Service Manual
This is the 66 pages manual for Jvc RXDV 31 SL Service Manual.
Read or download the pdf for free. If you want to contribute, please upload pdfs to audioservicemanuals.wetransfer.com.
Page: 1 / 66
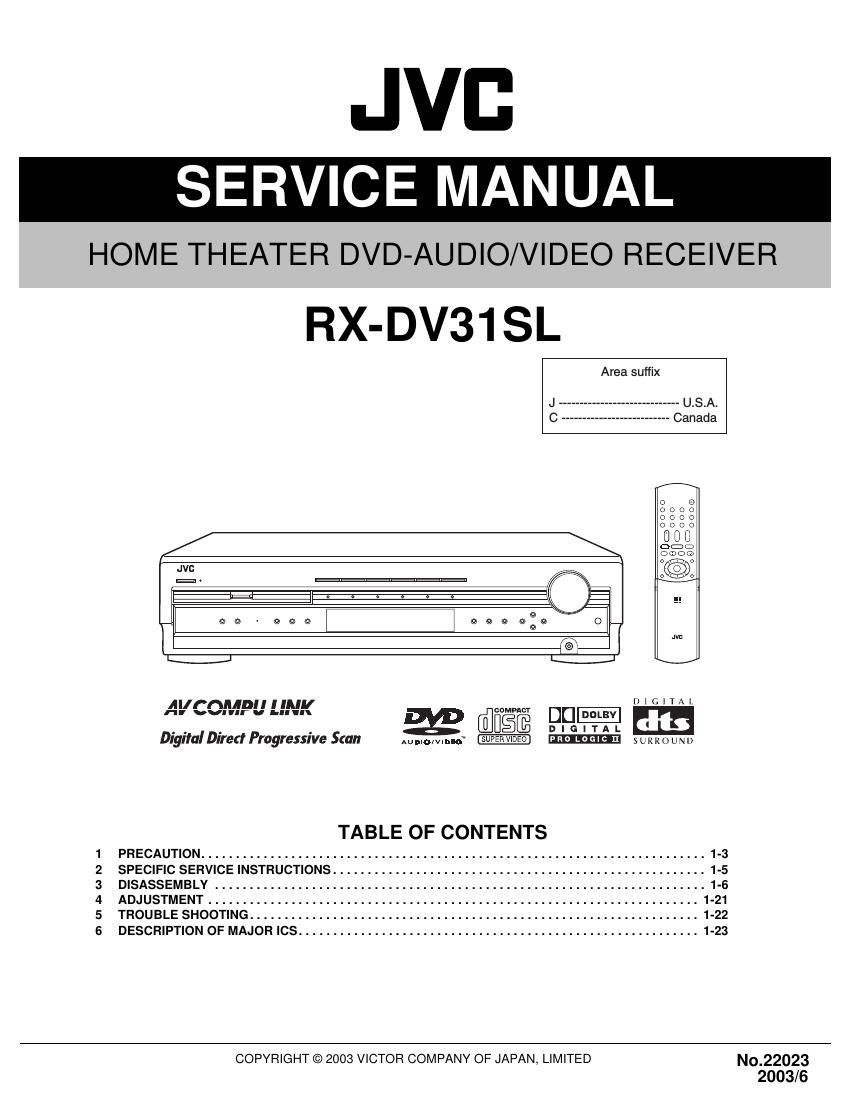