Jvc QLY 66 F Service Manual
This is the 28 pages manual for Jvc QLY 66 F Service Manual.
Read or download the pdf for free. If you want to contribute, please upload pdfs to audioservicemanuals.wetransfer.com.
Page: 1 / 28
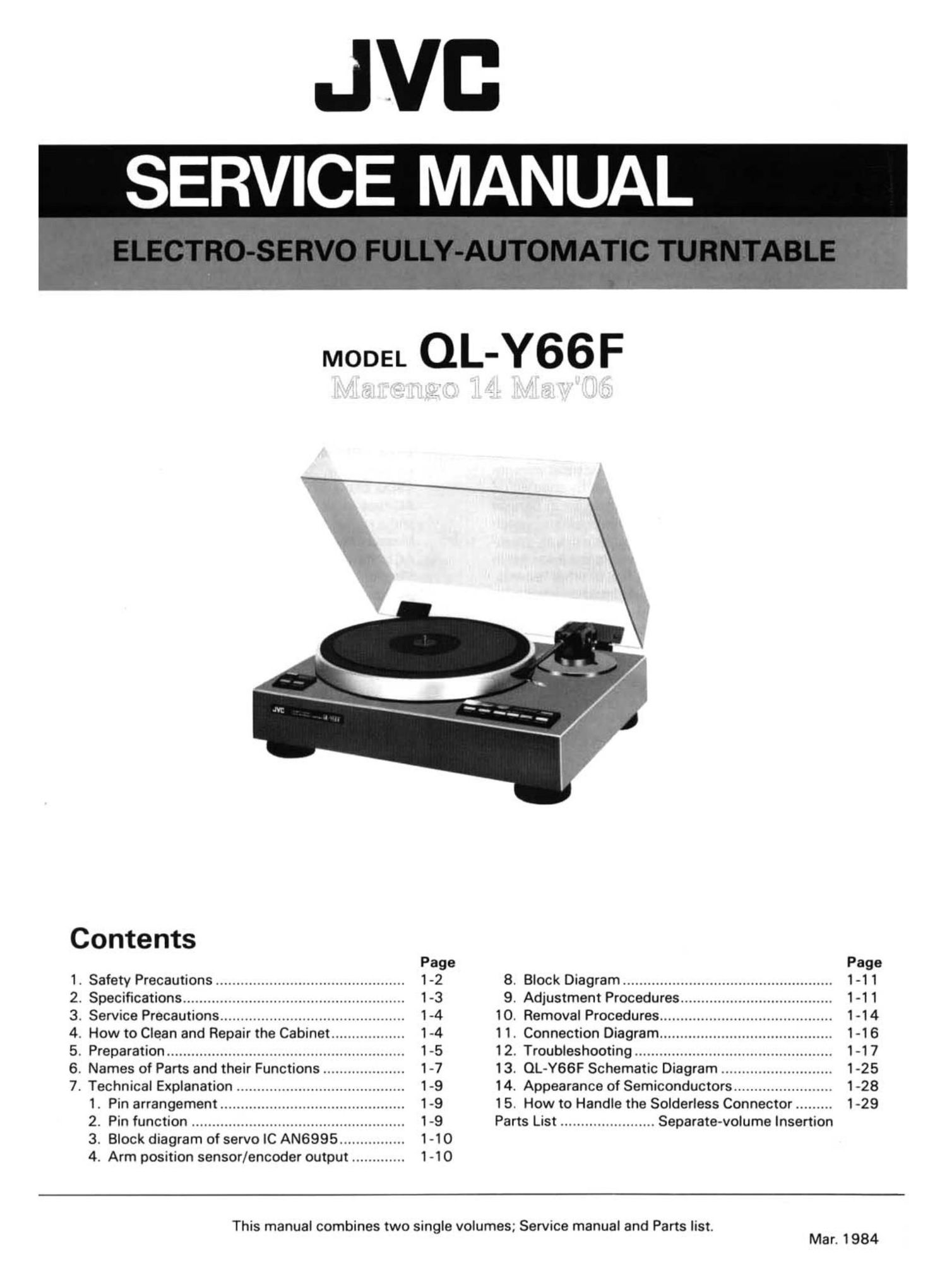