Jvc MC 8100 LU Service Manual
This is the 65 pages manual for Jvc MC 8100 LU Service Manual.
Read or download the pdf for free. If you want to contribute, please upload pdfs to audioservicemanuals.wetransfer.com.
Page: 1 / 65
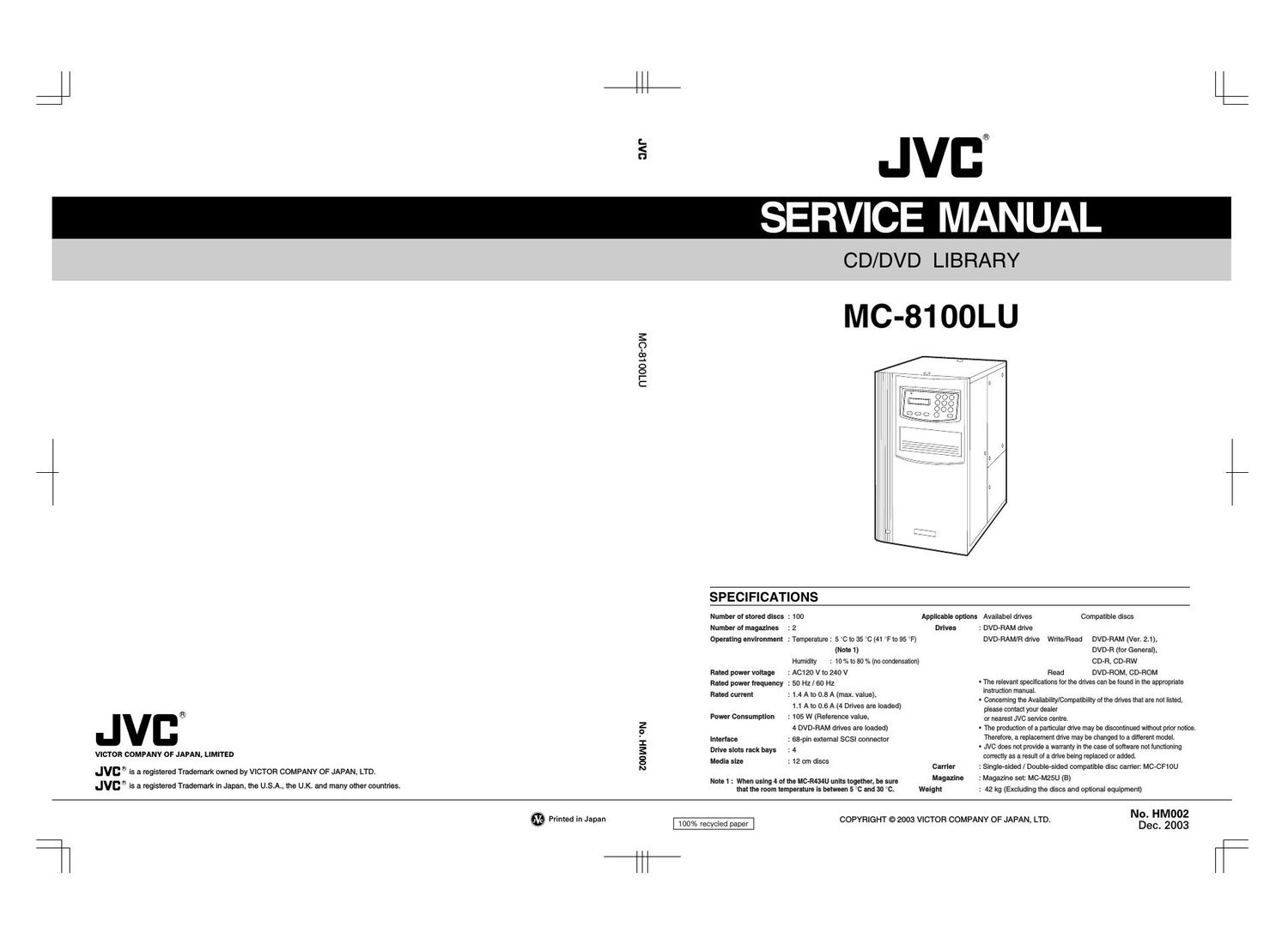