Jvc AXZ 911 BG Service Manual
This is the 65 pages manual for Jvc AXZ 911 BG Service Manual.
Read or download the pdf for free. If you want to contribute, please upload pdfs to audioservicemanuals.wetransfer.com.
Page: 1 / 65
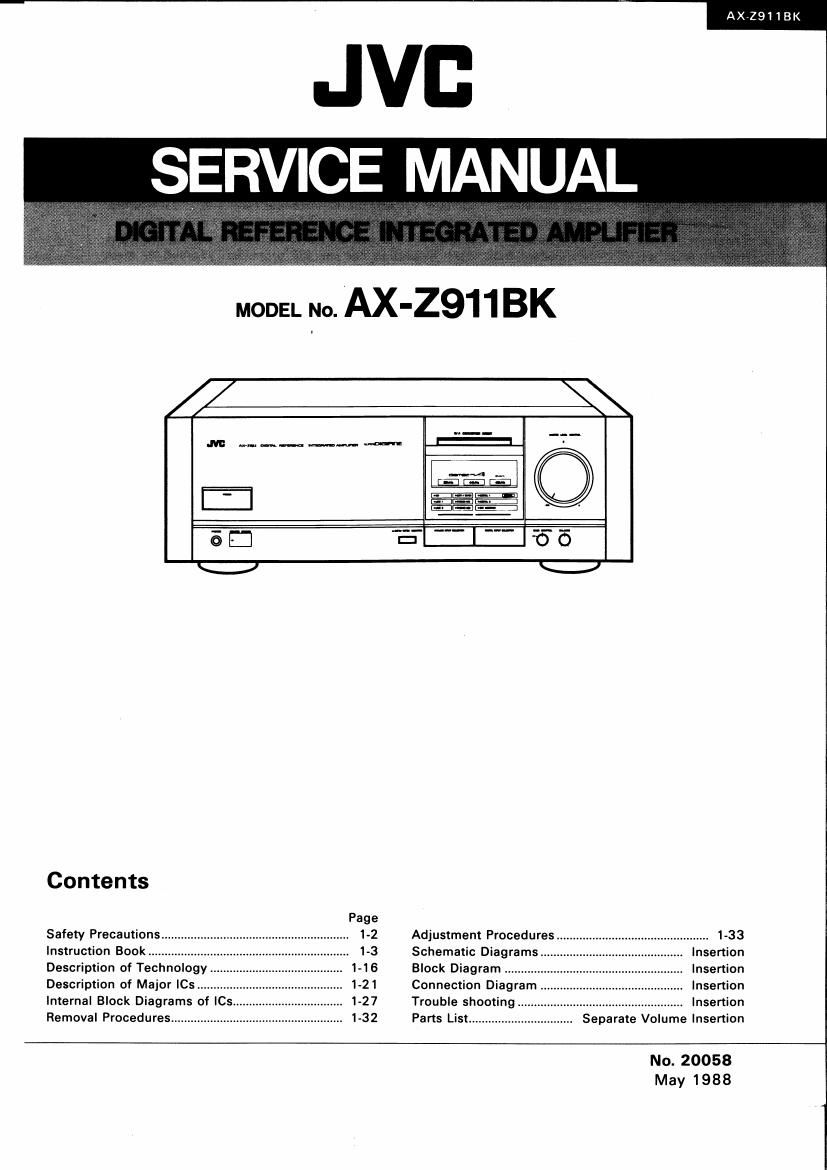