Heathkit HA 10 Schematic Manual
This is the 46 pages manual for Heathkit HA 10 Schematic Manual.
Read or download the pdf for free. If you want to contribute, please upload pdfs to audioservicemanuals.wetransfer.com.
Page: 1 / 46
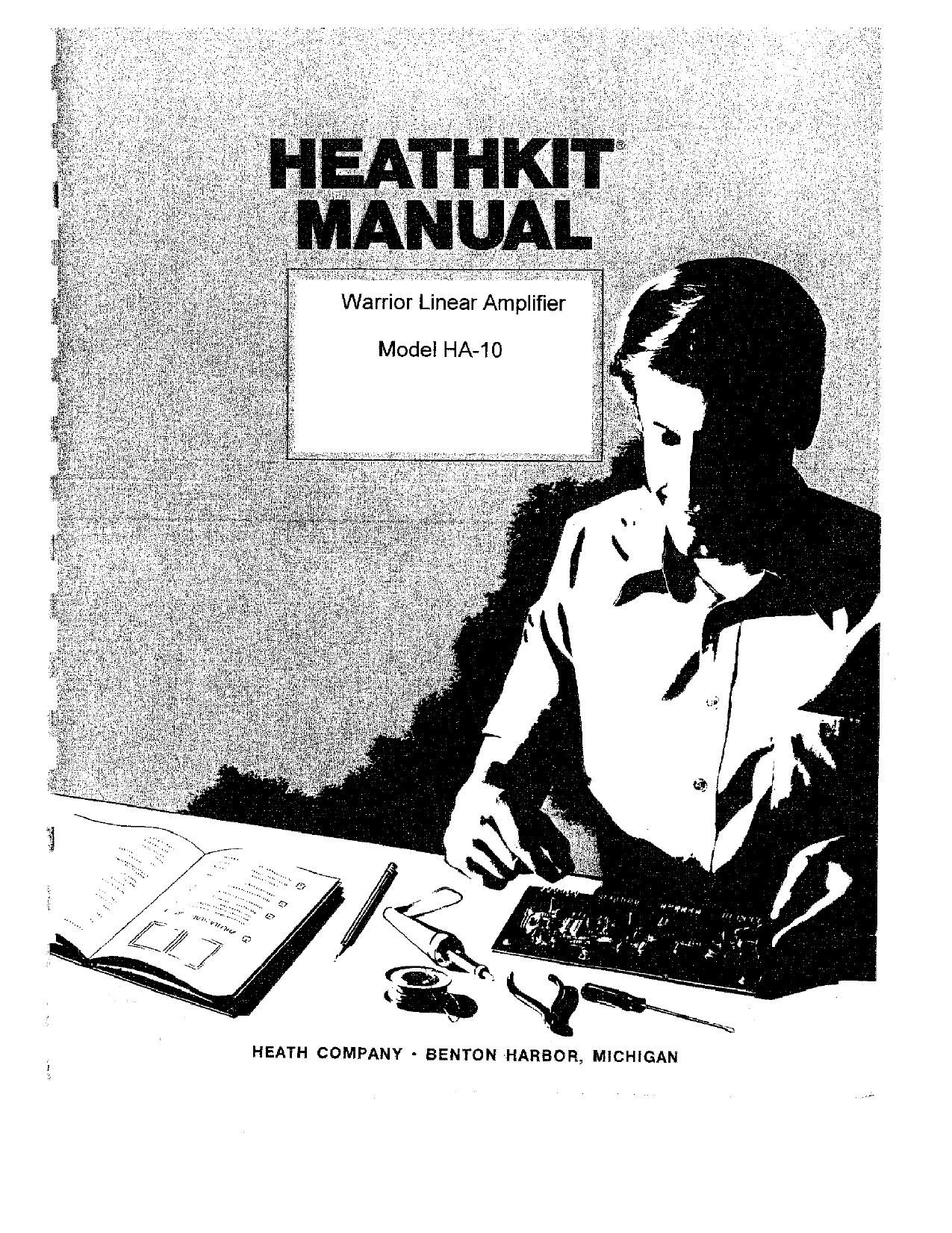