Heathkit H 10 Schematic Manual
This is the 156 pages manual for Heathkit H 10 Schematic Manual.
Read or download the pdf for free. If you want to contribute, please upload pdfs to audioservicemanuals.wetransfer.com.
Page: 1 / 156
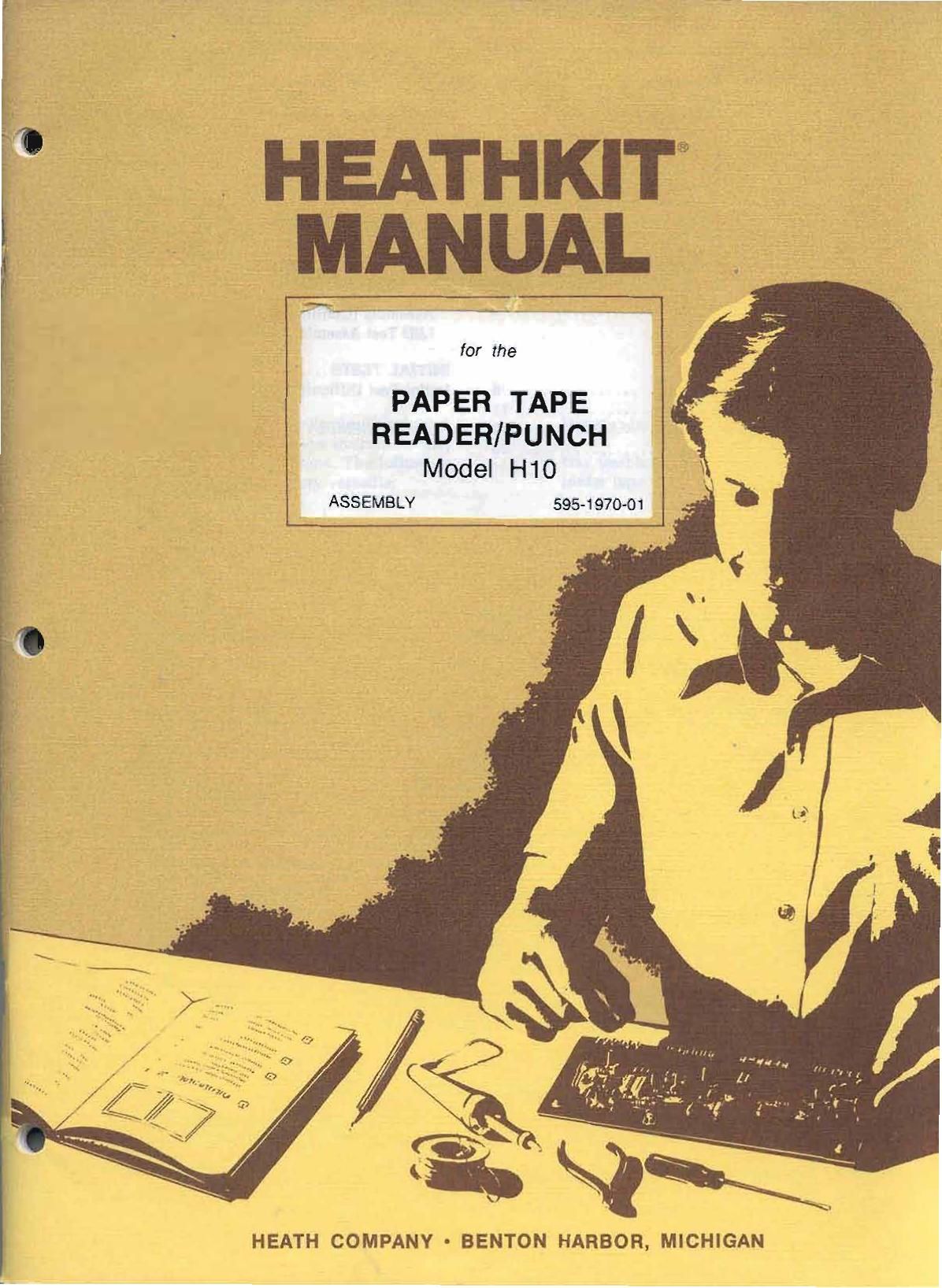