Heathkit FM 3A Manual
This is the 32 pages manual for Heathkit FM 3A Manual.
Read or download the pdf for free. If you want to contribute, please upload pdfs to audioservicemanuals.wetransfer.com.
Page: 1 / 32
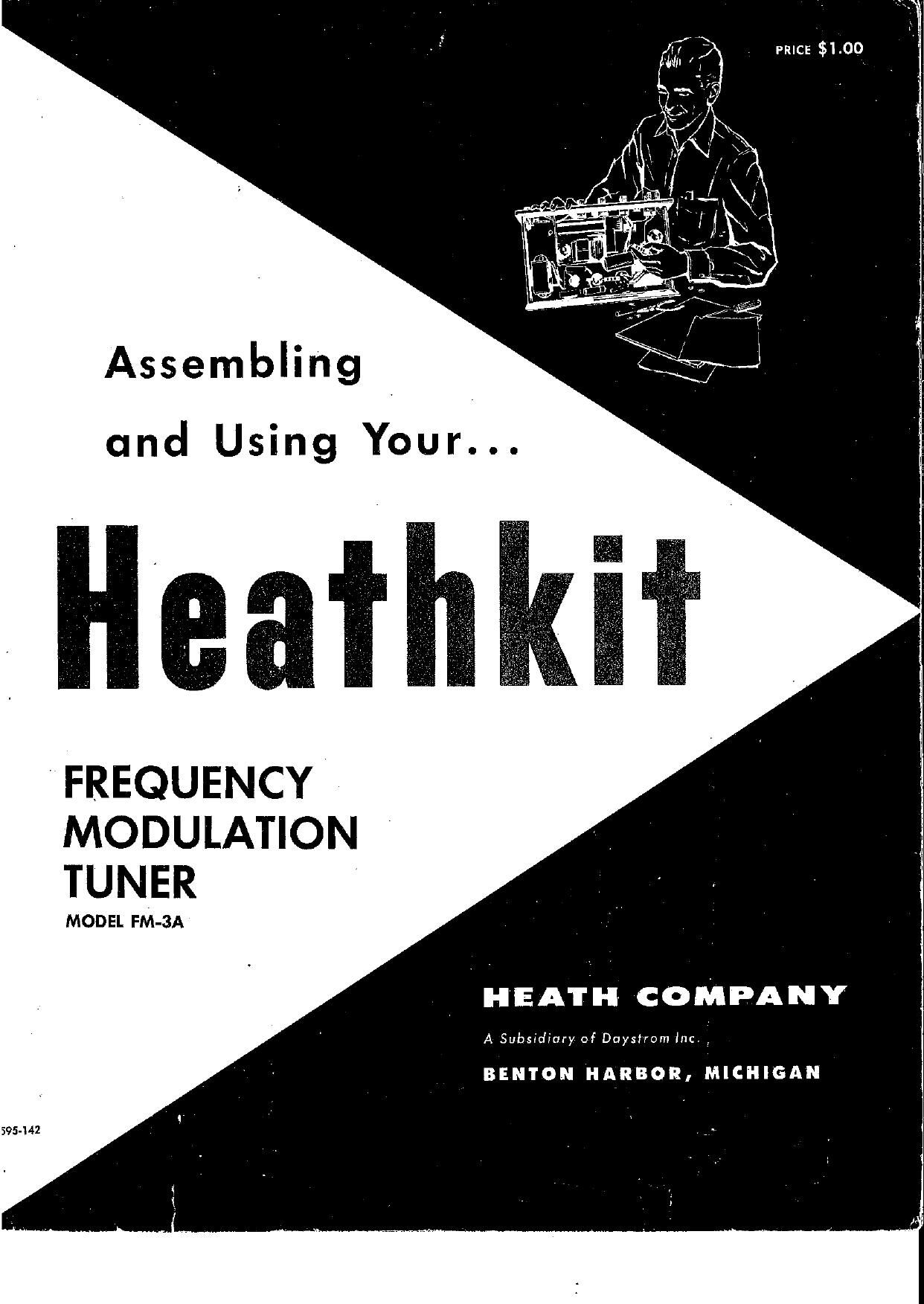