Ferrograph Y 722 Service Manual
This is the 74 pages manual for Ferrograph Y 722 Service Manual.
Read or download the pdf for free. If you want to contribute, please upload pdfs to audioservicemanuals.wetransfer.com.
Page: 1 / 74
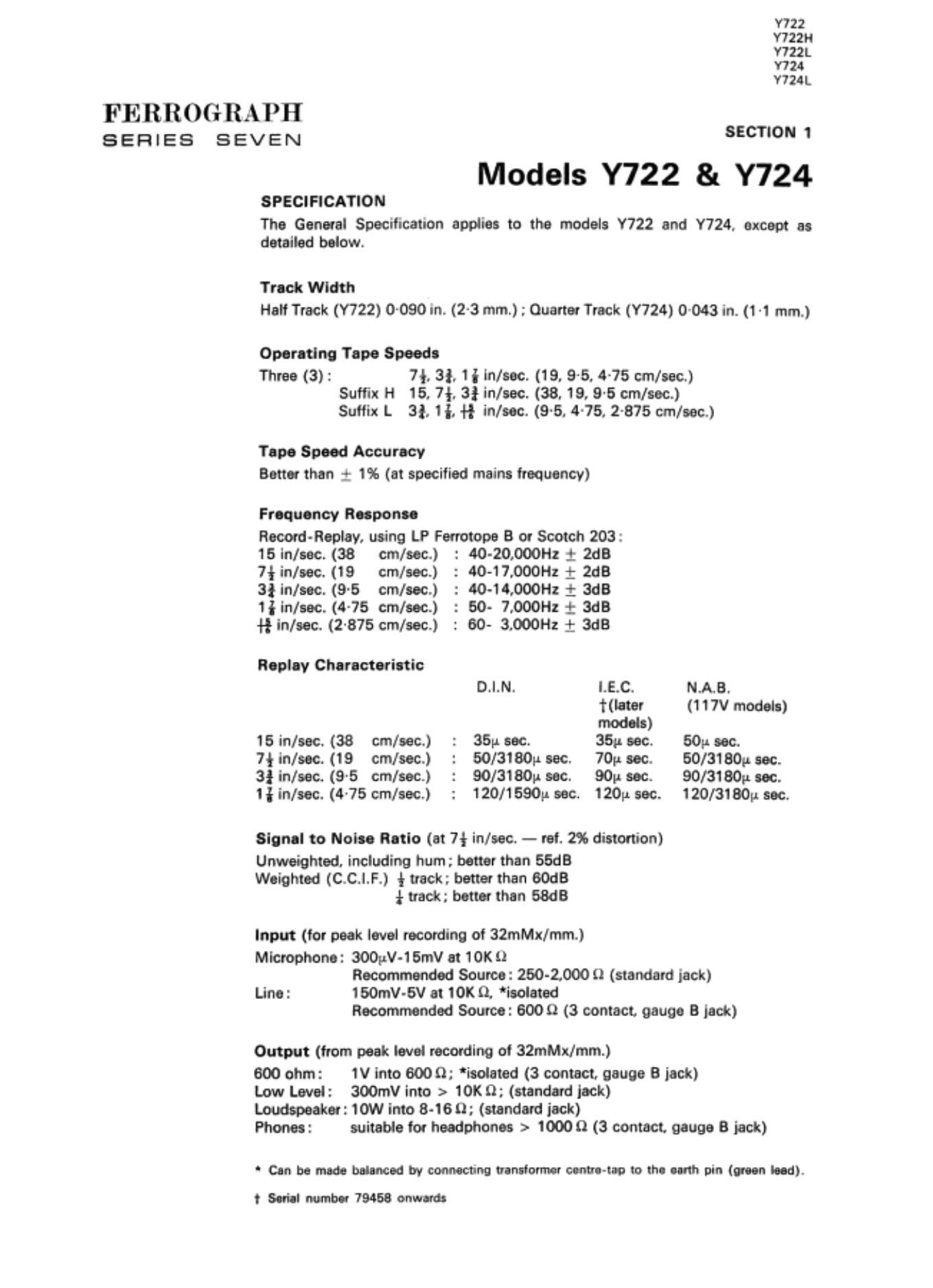