Crown Power Line One Service Manual
This is the 30 pages manual for Crown Power Line One Service Manual.
Read or download the pdf for free. If you want to contribute, please upload pdfs to audioservicemanuals.wetransfer.com.
Page: 1 / 30
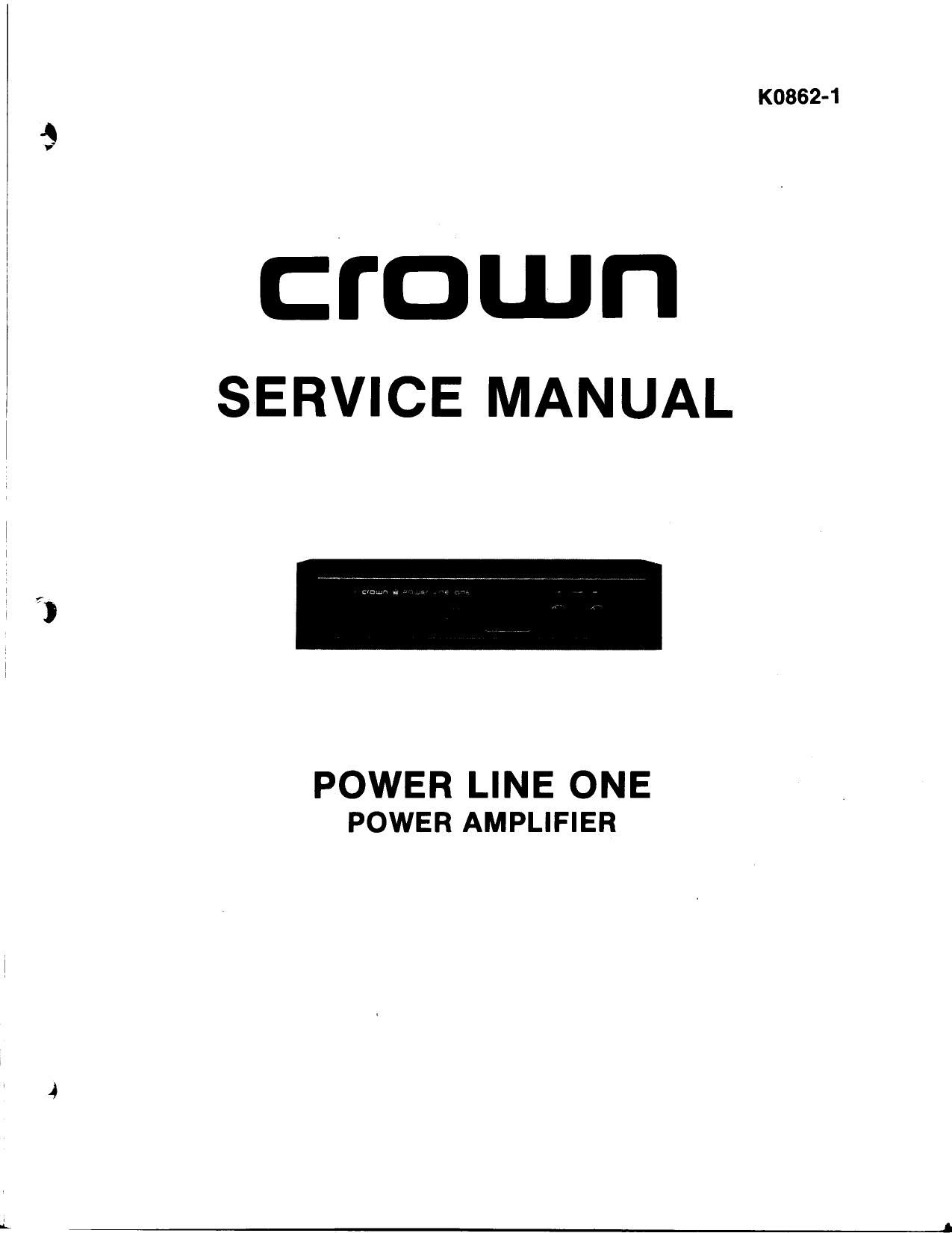