Akai GX 67 Service Manual
This is the 35 pages manual for Akai GX 67 Service Manual.
Read or download the pdf for free. If you want to contribute, please upload pdfs to audioservicemanuals.wetransfer.com.
Page: 1 / 35
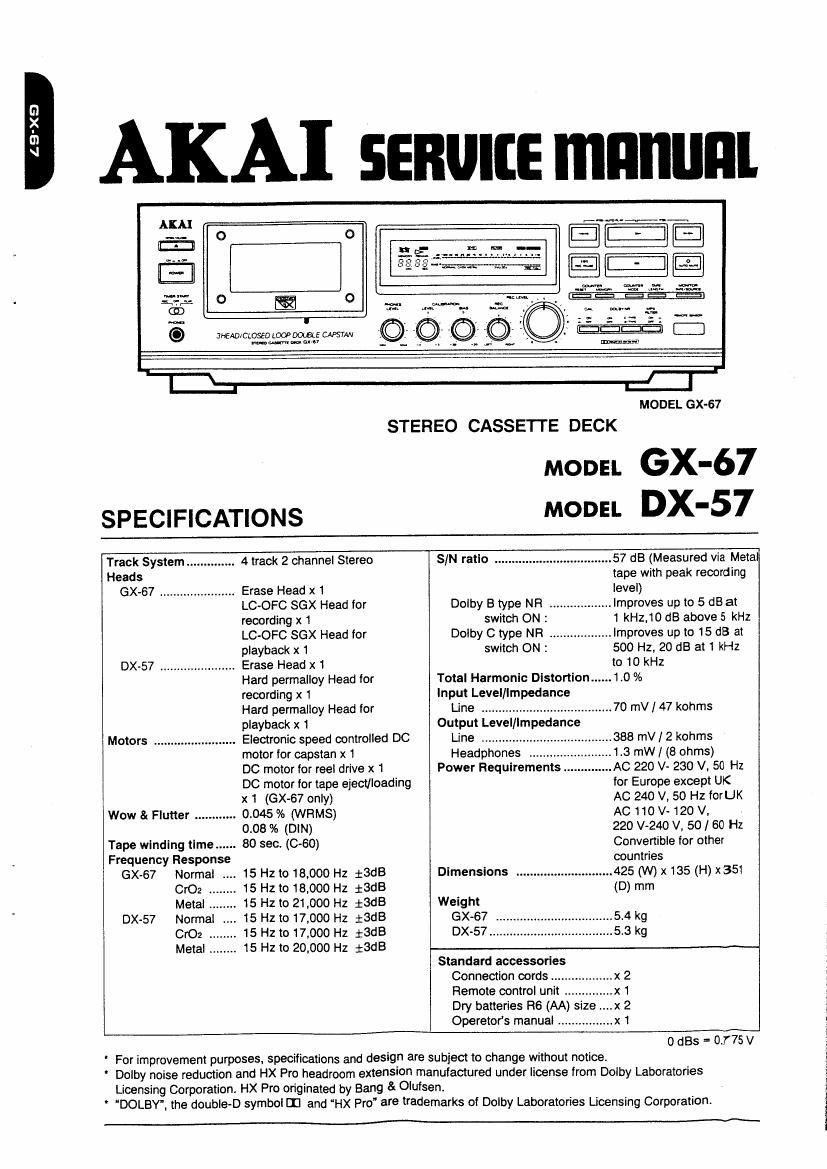